Эффективность функционирования предприятия, специализирующегося на реализации автозапчастей, в значительной степени зависит от организации складской логистики
20.03.2024 236 просмотров
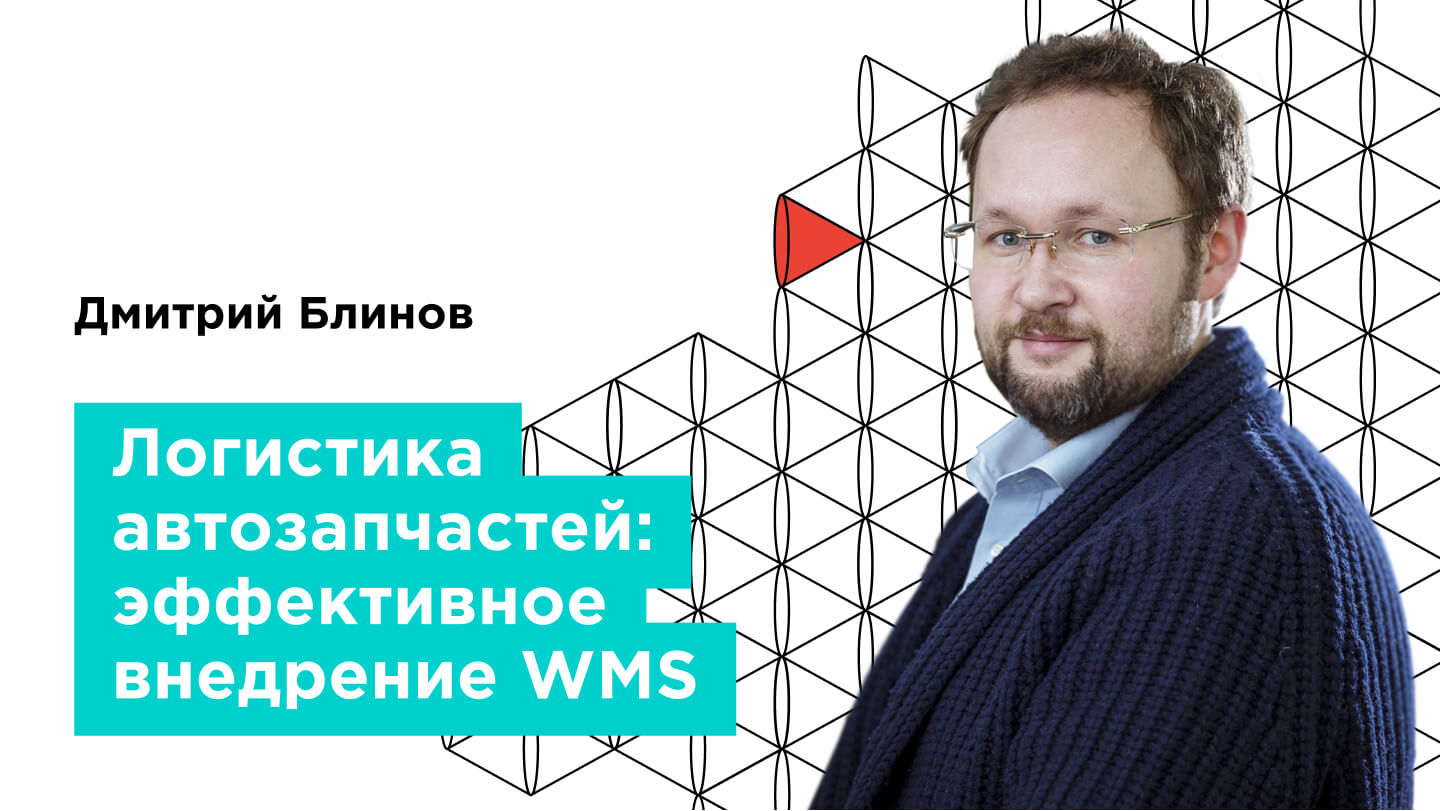
Эффективность функционирования предприятия, специализирующегося на реализации автозапчастей, в значительной степени зависит от организации складской логистики.
Очередной вебинар, который состоялся в рамках образовательного проекта GAZ Campus, был посвящен специфике склада запчастей и автоматизации логистических процессов. Спикером выступил технический директор группы компаний LogistiX — Дмитрий Блинов.
В чем заключается специфика склада автозапчастей?
- В разнообразии технологий хранения и видов груза в рамках одного склада. Это может быть как мелкоштучный, полочный товар, так и крупногабаритный товар.
- В обычных и специальных условиях хранения в рамках одного склада. Это могут быть и горючие жидкости, легковоспламеняемые и взрывоопасные изделия. То, что влияет на товарное соседство.
- В стандартном, количественно-штучном учете и дополнительных видах учета в рамках одного склада.
- В различных по категории прочности товарах в рамках одного склада.
- В многотысячном активном ассортименте — от десятков до сотен тысяч SKU*
(*SKU — идентификатор товарной позиции (артикул), единица учёта запасов, складской номер, используемый в торговле для отслеживания статистики по реализованным товарам/услугам). - В сезонном характере спроса по отдельным видам товара (аксессуары, шины).
- В дополнительных операциях в ходе приемки, хранения и отгрузки (фасовка, упаковка, маркировка и т. д.).
Эффективность использования WMS

Исследование Координационного совета по логистике показало, что ежегодно только 12% складов используют функциональные возможности системы более чем на 90% и более 80% складов используют их в пределах 15%.
Причина № 1, которая влияет на эффективность внедрения, — отсутствие качественного поставленной задачи, а также отсутствие качественного консалтинга в подготовке автоматизации.
Причина № 2 — справочники. Здесь два важных момента — не стоит, с одной стороны, недооценивать ситуацию, если у вас нет каких-то master-данных, с которыми система должна работать. В этом случае вы не сможете реализовать какой-то функционал и использовать его на складе. С другой стороны, стремление к тому, чтобы у вас всегда были все возможные данные, тоже бывает излишне.
В целом система должна поддерживать возможность работы как с полным объёмом весогабаритных характеристик, так и с частичным их присутствием.
И причина № 3 — отсутствие качественной подготовки к запуску именно на уровне проектной команды.
Почему возникает необходимость автоматизации склада?
Она возникает, когда склад уже не справляется с грузопотоком, который он обрабатывает. Если склад не справляется, первое что стоит сделать — провести аудит. Рекомендуется делать аудит следующего плана:
- Оцифровать ваши потоки, провести их анализ;
- Оцифровать ваши потоки, провести их анализ;
- Формализовать ваши процессы;
- Определить, насколько ваши процессы соответствуют вашим потокам. То есть способны ли вы, за счет имеющегося ресурса и выстроенных технологических процессов, эти потоки обработать и понять, сколько у вас резерва мощности.
Только после этого у вас могут появиться требования к системе управления складом.
Как из догоняющего стать опережающим?
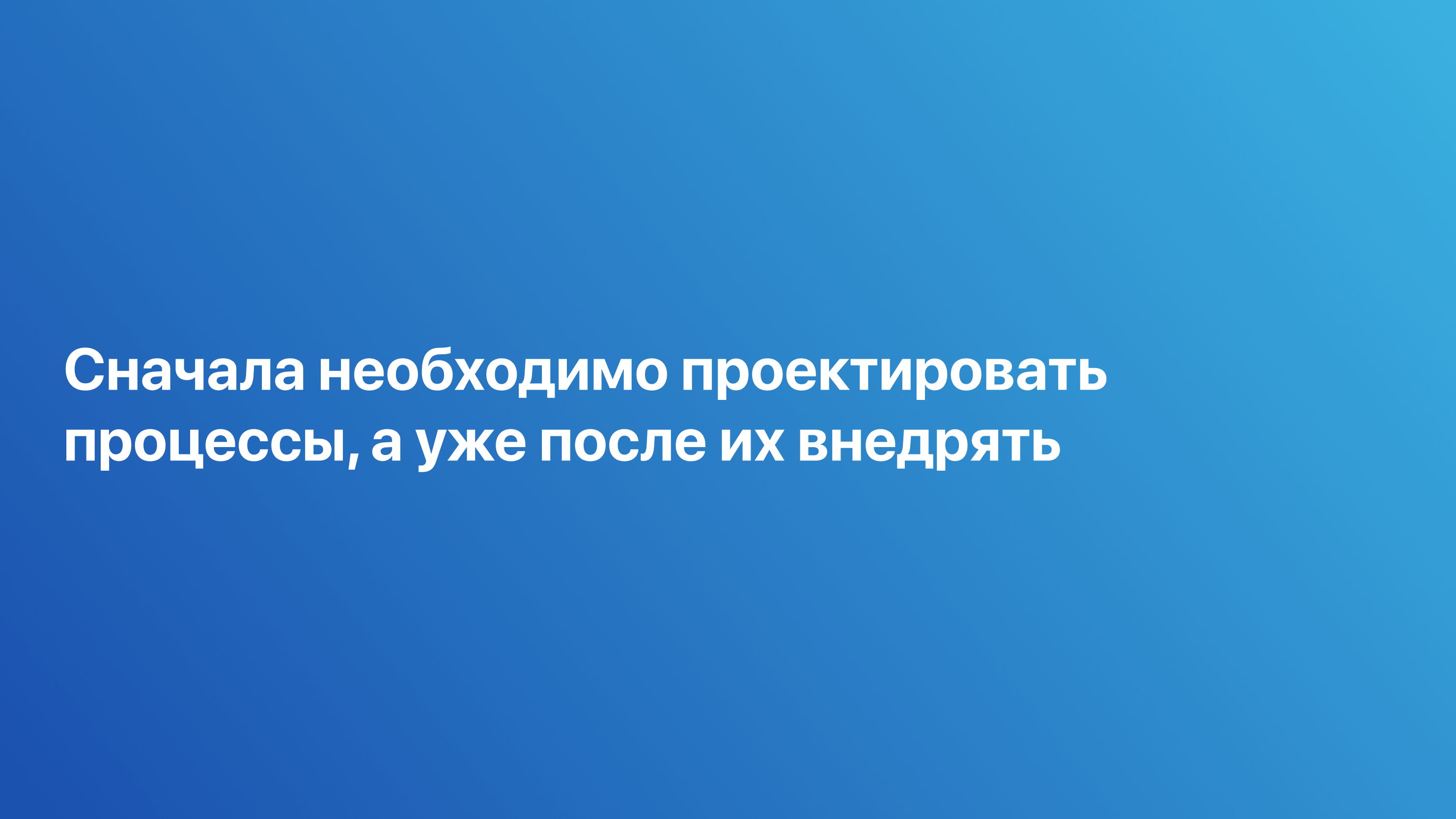
Сначала необходимо проектировать процессы, а уже после их внедрять. Компания должна превратиться в механизм для реализации идей. Проще говоря, у вас возникла идея, вы эту идею донесли до сотрудников, декомпозировали до конкретных процессов, процессы внедрили, и команда благополучно всё это исполняет.
Что делает догоняющая компания? Догоняющая компания пишет бизнес-процессы вдогонку практическому исполнению на складе. То есть работают в режиме «казаться, а не быть». Часто встречается ситуация, когда у компании внедрен 5С, бережливый склад, бережливое производство, но результат работы при этом зависит не от стандартов, а от конкретных людей. Со временем уровень качества работ ожидаемо снижается, а компания не умеет использовать новые инструменты работы.
Опережающие компании работают по циклу, они проектируют бизнес-процессы в соответствии с товаропотоком, то есть работают в парадигме «быть, а не казаться». В этом случае важен не конкретный исполнитель, а модель управления. Передача знаний всегда подкрепляется инструкциями, процессы всегда стабильны и обеспечивают заданный уровень качества.
Этапы подготовки к автоматизации включают в себя:
- Организацию проектной команды. Не рекомендуется сводить всю ответственность к одному человеку. Эффективнее распределять ответственность между разными пользователями. Это помогает сотрудникам лучше понимать процессы, за которые он отвечает на складе;
- Проведение расчетного аудита на предмет соответствия текущего и перспективного товаропотока существующим на складе бизнес-процессам, оборудованию и исполняющим ресурсам. Фиксацию рисков и рекомендаций по отношению к каждому бизнес-процессу;
- Обеспечение достоверности используемых справочников; устранение неэффективностей, связанных с технологией и топологией склада.
Этапы подготовки к автоматизации включают в себя:
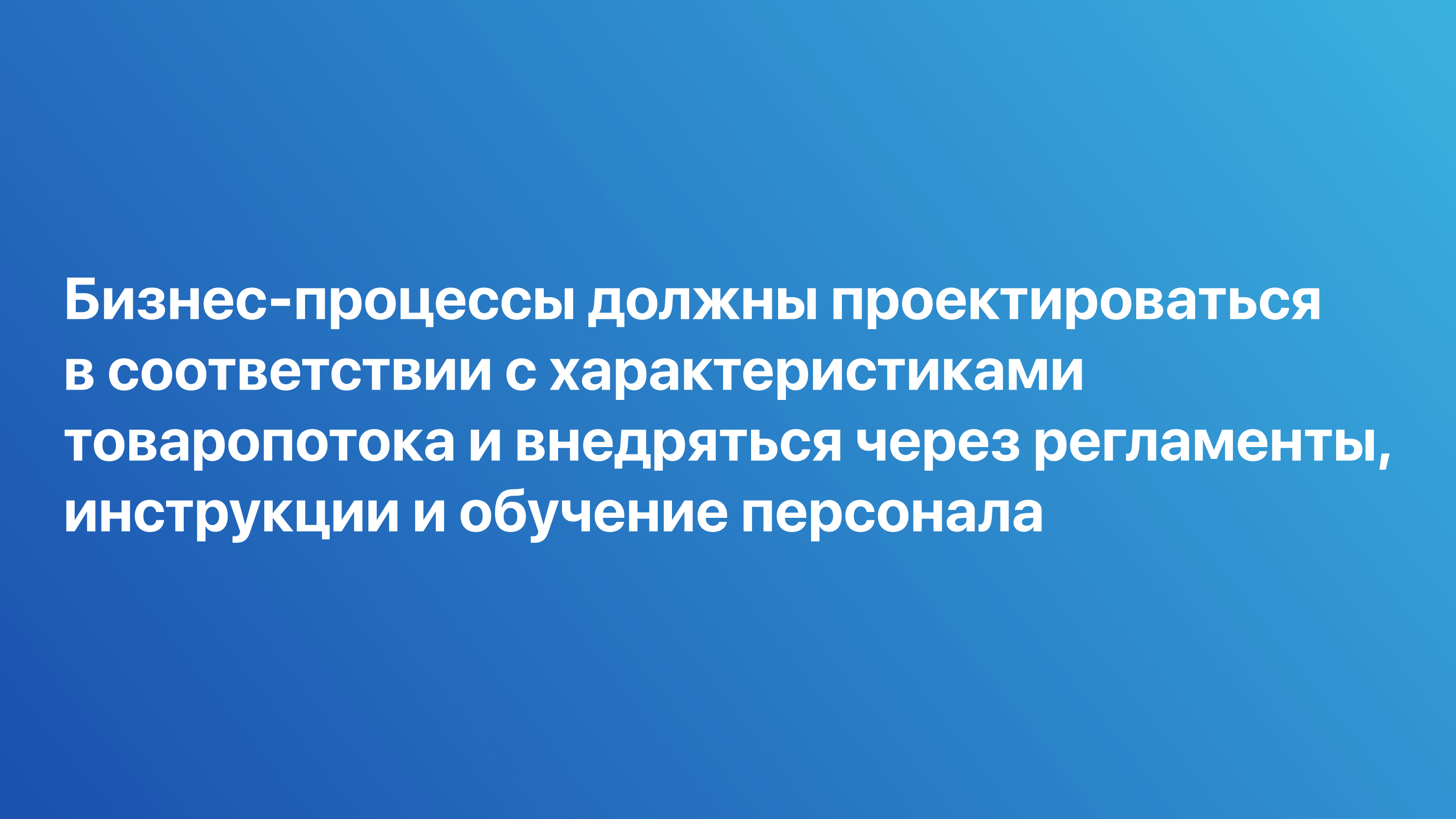
Чтобы корректно управлять изменениями в рамках процесса автоматизации склада, необходимо учитывать нынешние технологические процессы, знать целевые технологические бизнес-процессы, чтобы понимать, какие организационные изменения нужно предпринять.
- Оценка рисков. Привлекайте отраслевую экспертизу, чтобы увидеть, где процесс может быть выстроен некорректно.
- Обучение ключевых пользователей. Постарайтесь сначала обучить пользователей. Если сначала обучить персонал, а после делать функциональную приемку системы — это будет проще и выгоднее.
- Участие в опытной эксплуатации. Важный нюанс, потому что вопросы пользователей системы (сотрудников, линейного персонала, всех задействованных) должны быть адресованы не консультанту, присутствующему на объекте, а в большей мере эти компетенции необходимо переносить на себя, чтобы иметь возможность самостоятельно отвечать на вопросы линейных сотрудников.
Устранение неэффективности в части оборудования
Системы хранения мелкоштучного товара
Для каждой группы товаров есть рекомендуемая система хранения грузообработки. Например, мелкоштучную группу товаров хранят либо в контейнерах на полочных стеллажах, либо на полочных стеллажах, на вертикальных или горизонтальных каруселях, или в контейнерных магазинах. Это, по большому счету, отраслевые, стандартные подходы, которые используются на большинстве предприятий, в том числе, за рубежом.
Полочный товар и товар на крючках
Полочный товар — тот, что хранится выкладкой. Под каждую группу таких грузов предполагаются свои системы хранения, то есть полочный штучный товар, товар на крючках, полочный стандартный товар. Соответственно, если у вашего автоматизатора есть отраслевая экспертиза, то он раскладывает ваш ассортимент по товарным группам, и вы понимаете, в каком объеме каждая товарная группа представлена, соответственно, понимаете, сколько вам нужно того или иного оборудования и насколько рационально это оборудование используется.
Паллетный стеллажный товар
Стандартные, конвейерные запчасти, товары в клетях. Соответственно, крупногабаритные товары: рамы, шасси, кабины, кузова и так далее.
Штабельный и фреймовый товар
Здесь важно, чтобы система управления складом, которую вы выбрали, поддерживала для каждой такой отдельно взятой системы хранения свои специфические стратегии. Потому что, как ни странно, в штабельном хранении очень часто используется далеко не одна стратегия формирования штабеля. Поэтому все зависит от процессов. Сначала вы провели необходимый аудит, выявили товарные группы, провели отраслевую экспертизу и дальше сможете понять, какие изменения нужно сделать на складе, чтобы прийти к элементам порядка.
Каждое оборудование выбирается под конкретную технологию, то есть, вы выбрали какое-то оборудование системы хранения для конкретной группы товаров, выбрали систему грузообработки, и только после этого можете сказать, какое оборудование необходимо здесь применить. Вот это лучший подход. Не стоит пытаться на первых этапах быстро закупить оборудование, делать это необходимо очень вдумчиво и с учетом всех имеющихся у вас требований.
Сценарий внедрения WMS
Есть 4 базовых сценария.
Impact. Метод рассчитан и на новые, и на модернизируемые объекты, и подразумевает запуск сразу всех зон и процессов единовременно, с максимально возможным уровнем стресса, и предельно быстрым выходом на плановый уровень производительности. Из проблем — высочайшие риски и возможность финансовых и репутационных потерь.
Process-by-Process. Вариант, когда последовательно автоматизируются разные процессы, начиная от приемки, и заканчивая вторичными отчетами, оптимизацией и другими дополнительными функциями. Такой вариант позволяет быстро оценить результат каждого конкретного этапа, внести необходимые изменения, и двигаться дальше. Из минусов — увеличенные сроки внедрения.
Zone-by-Zone. Последовательный охват полным функционалом систем разных зон склада. Если начать автоматизацию с наименее загруженных зон склада, и провести там обучение персонала с ротацией сотрудников, можно обеспечить выход на промышленную эксплуатацию объекта с минимальным стрессом. Из минусов — так как разные зоны обычно связаны с разными группами товаров, есть вероятность, что в определенных зонах возникнет необходимость оперативно донастраивать функциональную часть, а также расширять сопровождение, так как могут возникнуть ситуации, с которыми сотрудники в других зонах не сталкивались.
Day-by- Day. Подходит только для новых объектов. Практически идеальный вариант, когда нагрузка на склад планомерно возрастает, давая возможность сотрудникам адаптироваться к изменившимся условиям и новой технологии грузообработки. Минус — увеличение срока возврата инвестиций по складскому комплексу, необходимость постоянного мониторинга ритмичности и нагрузки, а также привыкание персонала к сниженной нагрузке, что приводит к кадровым изменениям после выхода на плановую производительность.
Тестирование системы
Тестирование системы можно разделить на три этапа:
- Техническое тестирование. Первичное тестирование компонентов системы на работоспособность посредством отправки массива параметров на вход и проверки выхода на ожидаемый результат. Реализуется исполнителем.
- Функциональное тестирование. Проверка соответствия реакции системы на зафиксированные действия пользователей, систем и события. Система должна обеспечивать возможность выполнения каждого автоматизированного технологического процесса. Реализуется исполнителем, впоследствии — заказчиком для приемки системы.
- Нагрузочное тестирование. Отправка в систему избыточного количества заданий с проверкой реакции каждого ассоциированного с тем или иным технологическим процессом компонента системы на предмет соответствия документу постановки задач. Опционально реализуется исполнителем и/или заказчиком при наличии такой необходимости или зафиксированных обязательств.
Подведение итогов и оценка полученных результатов
После проведения полноценного проекта с реинжинирингом бизнес-процессов, с автоматизацией по складскому персоналу, по использованию трудовых ресурсов и складской техники, можно увидеть изменения следующих показателей:
- уменьшение количества ошибок отбора,
- снижение потерь просроченного товара,
- уменьшение простоев,
- увеличение пропускной способности.
Это, пожалуй, типовые целевые показатели, к которым имеет смысл стремиться.